As the world is moving toward a greener tomorrow, paper bag factories are gaining popularity as businesses and consumers move away from plastic. Be it a shopping mall or just common shops, people prefer sustainable options, and that is paper bags. However, maintaining quality, safety, and compliance in paper bag manufacturing is important for meeting industry and regulatory standards. BRCGS Certification (Brand Reputation through Compliance of Global Standards) is one of the most recognized benchmarks for quality, safety, and operational compliance, and BRCGS certification for paper bag factories can be game-changing.
This guide gives you insights into everything you need to know about BRCGS Certification for paper bag factories, including industry trends, compliance requirements, cost breakdown, challenges, solutions, and case studies.
The Growing Demand for Paper Bags
You are already aware of how the paper bag industry is expanding its horizons to a greater level because of the rising concern of environmental issues. According to market reports:
- The global paper bag market is projected to grow at a CAGR of 4.5% from 2023 to 2030.
- Countries like India, the USA, and the UK are enforcing stricter bans on single-use plastic, boosting the demand for paper bags.
- You might see clearly that some famous brands like McDonald’s, Starbucks, and Amazon have taken the first move towards a better tomorrow by using paper bags.
With this growing demand, paper bag factories must make sure that their products meet global safety, hygiene, and quality standards. This is where BRCGS Certification for paper bag factories becomes a key factor.
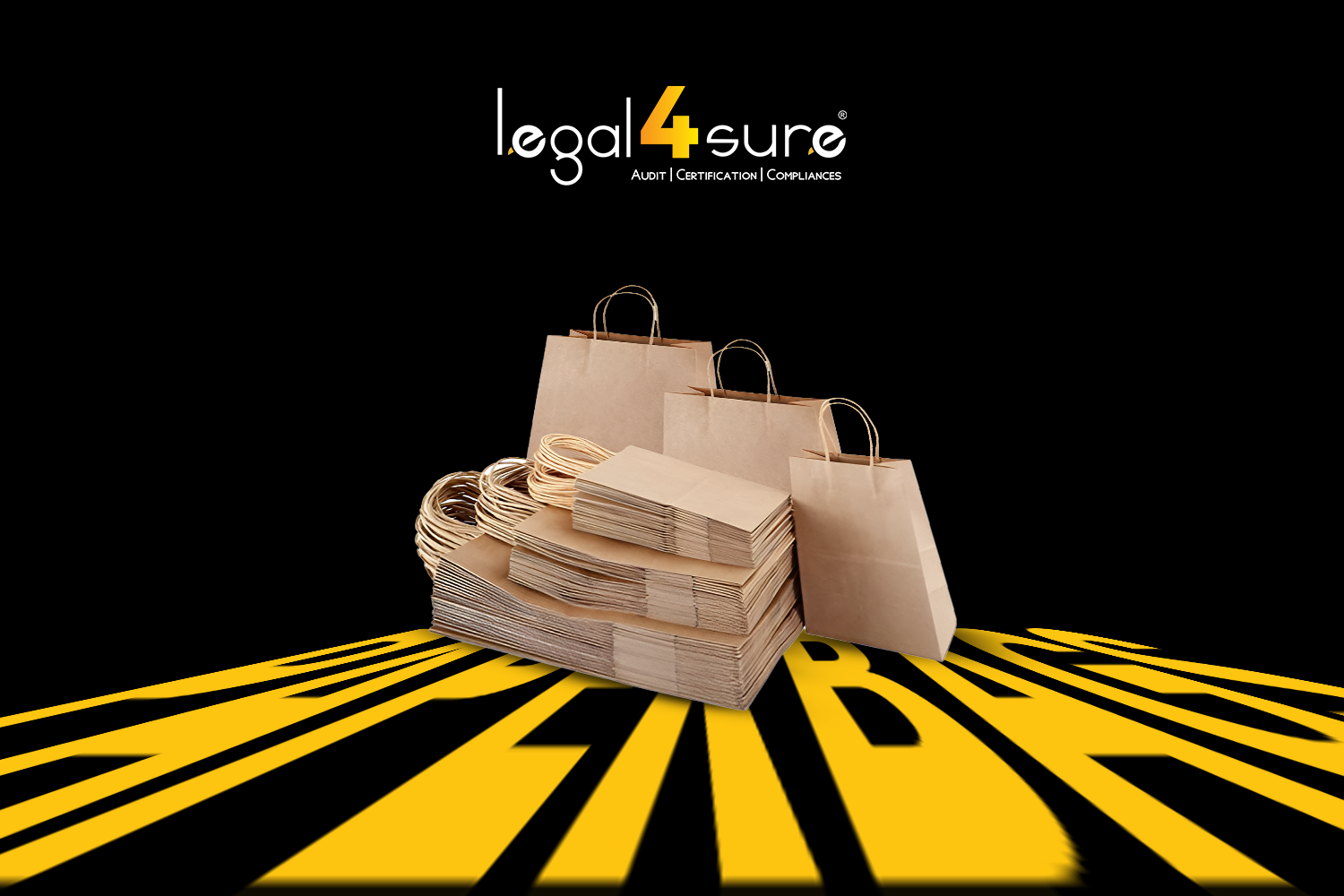
Why BRCGS Certification is Important for Paper Bag Factories
Now you have a clear picture of how paper bags are important in today’s world. And now, what can BRCGS Certification do for paper bag factories? Brcgs certification helps manufacturers to show compliance with international quality and follow safety standards. Here are the key benefits:
- Keeps products safe and reliable: This certification helps you maintain hygiene in raw materials, adhesives, and printing processes. Give more opportunities.
- Makes it easier to sell worldwide: This certification is required by retailers and brands worldwide.
- Helps work get done faster and better: BRCGS certification makes sure you follow best practices in manufacturing and supply chain.
- Helps to gain industry recognition The one of the most important, BRCGS certification for paper bag factories will increases consumer trust, and helps in business expansion.
- Keeps up with industry guidelines: BRCGS packaging certification helps businesses comply with ISO, FDA, and EU packaging directives.
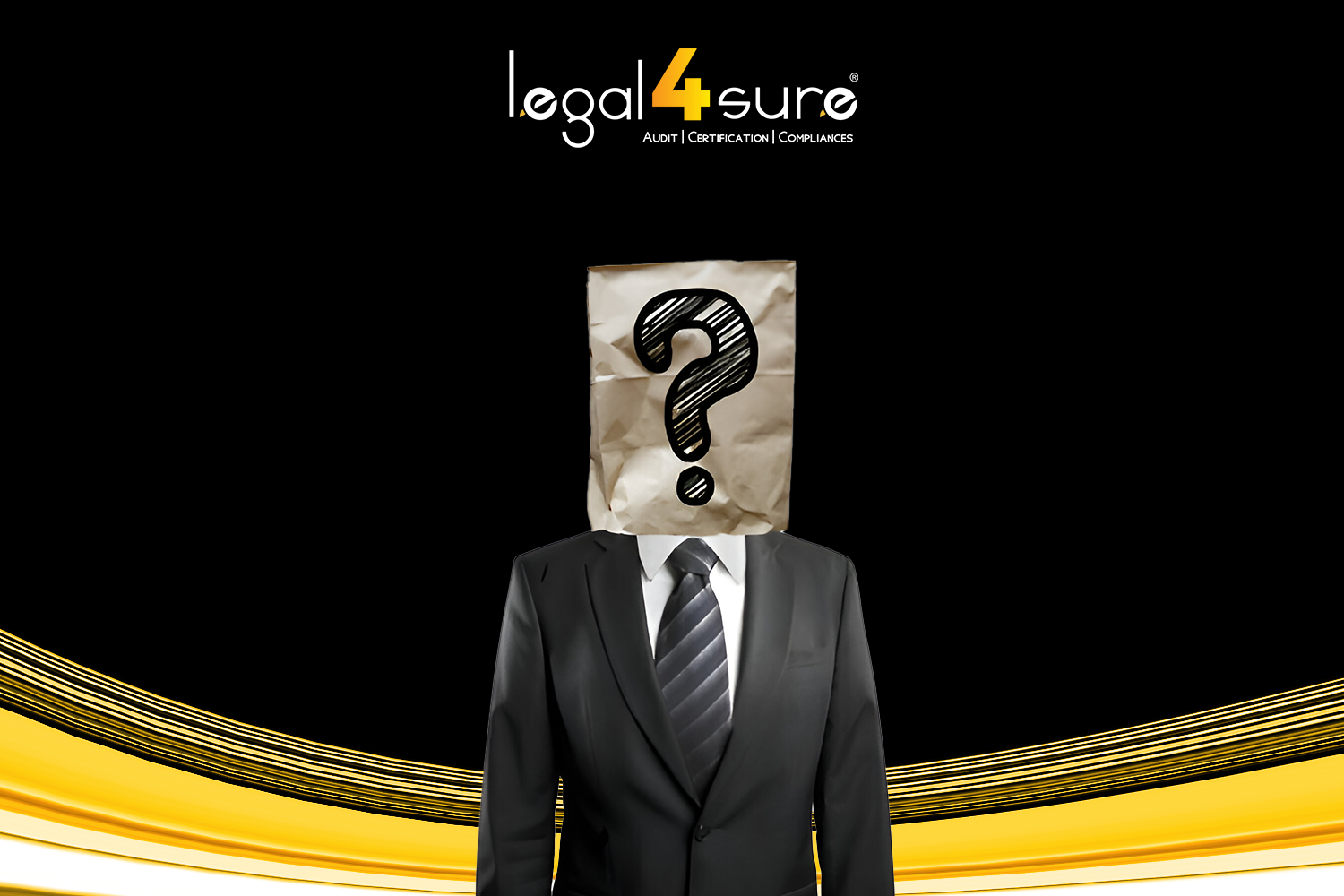
Challenges Faced by Paper Bag Factories in Achieving BRCGS Certification & Solutions
Challenge 1: Making sure products are always top quality
- Issue: Variations in raw materials, adhesives, and ink quality lead to inconsistencies in paper bags.
- Solution: The best way to deal with it, is to implement strict supplier quality checks and standardized production processes to make sure better workflow and uniformity prevail.
Challenge 2: Keeping hygiene and safety a top priority
- Issue: Paper bags used in food and retail packaging must follow hygiene practices and safety norms.
- Solution: To deal with this, set up clean zones in manufacturing units, train your employee properly, and conduct regular audits to comply with BRCGS hygiene requirements.
Challenge 3: Planning certification costs wisely
- Issue: Small and mid-sized manufacturers may face some issues related to cost compliance.
- Solution: A BRCGS consultant helps you in every manner. They start with a gap analysis, help you with better process flow, and opt for government subsidies or industry grants to ease financial issues.
Challenge 4: Documentation and Record-Keeping
- Issue: BRCGS certification requires detailed documentation of processes, material sourcing, and audits.
- Solution: Use automated compliance software to track and maintain records efficiently.
Challenge 5: Employee Training & Awareness
- Issue: Lack of awareness among employees about BRCGS protocols can lead to non-compliance.
- Solution: Conduct regular training programs, create easy-to-follow SOPs, and encourage employees to follow best practices in manufacturing and hygiene.
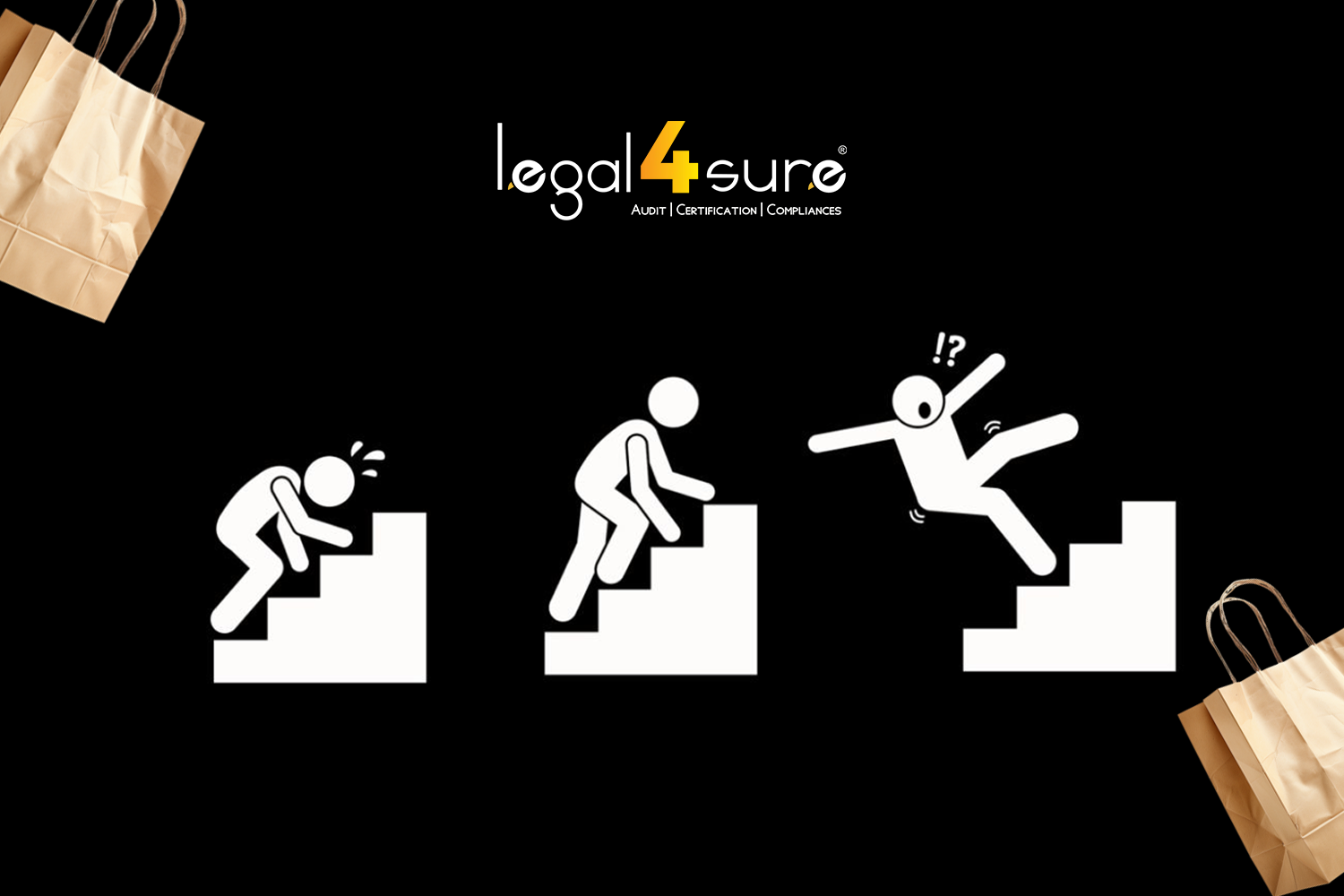
For Indepth Information Click Here: Challenges In BRCGS Certification Audit
Requirements for BRCGS Certification in Paper Bag Manufacturing
What are the main requirements for paper bag factories to achieve BRCGS certification? This section will help you to know more about BRCGS Certification in paper bag manufacturing. They must meet the following standards:
1. Quality Management System (QMS)
- Documented policies, SOPs, and record-keeping.
- Clear responsibilities for quality control teams.
2. Hazard and Risk Analysis (HACCP)
- Checking for anything harmful in raw materials, glues, and inks.
- Take steps to keep products clean and safe.
3. Hygiene and Safety Standards
- Making sure raw materials are safe and free from harmful chemicals.
- Keeping things clean and safe.
- Following rules for safe food packaging.
4. Supplier and Material Control
- Using paper from trusted, certified sources (like FSC-certified paper).
- Following EU and FDA rules for safe food packaging.
5. Production Process Compliance
- Doing regular checks to make sure the paper is thick, strong, and long-lasting.
- Use safe methods for printing and labeling.
- Following eco-friendly and sustainability guidelines.
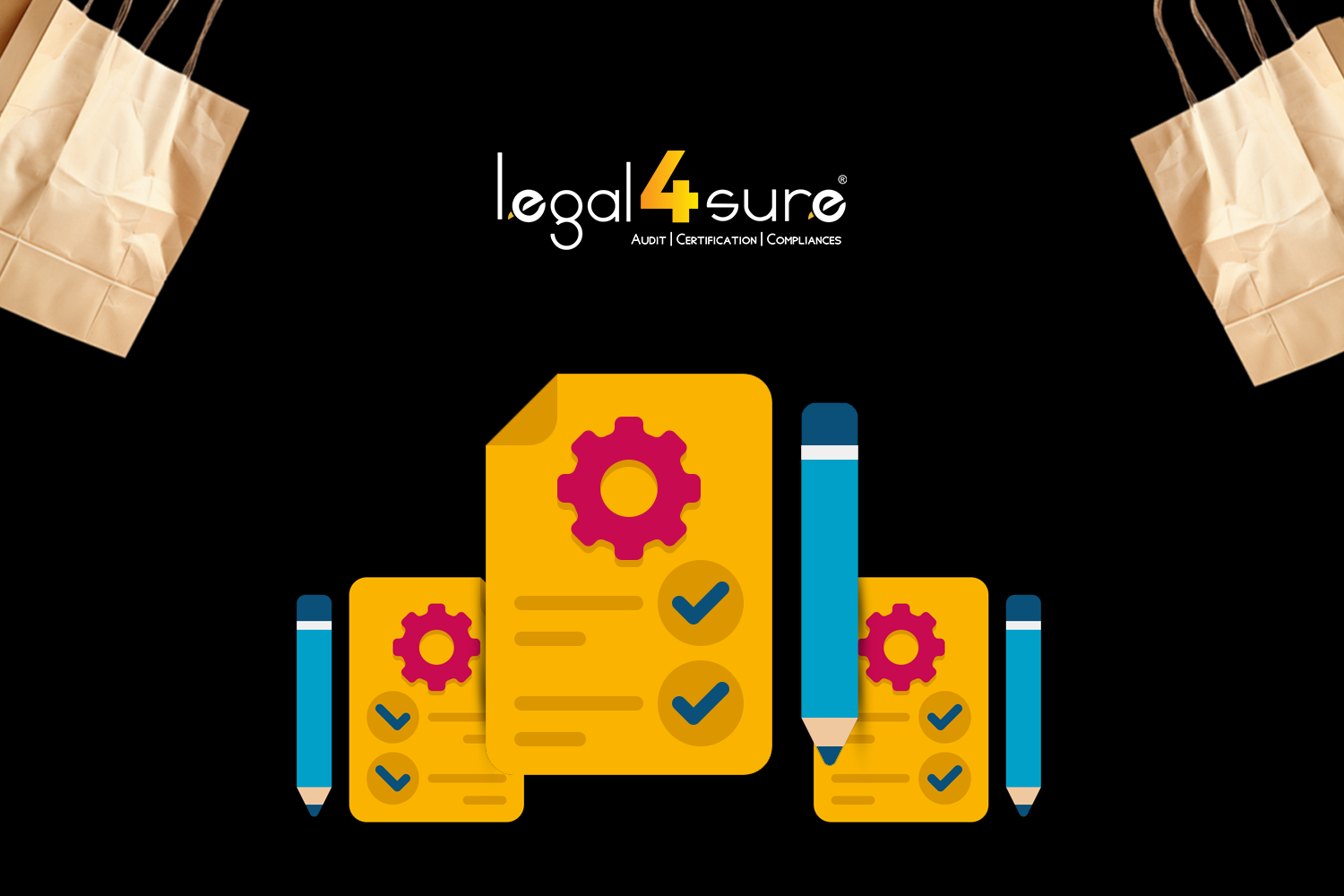
To Know More: BRCGS Food Packaging Certification
Cost Breakdown of BRCGS Certification for Paper Bag Factories
BRCGS certification costs depend on several factors, such as factory size, number of employees, and challenges of operations. Below is an estimated cost structure:
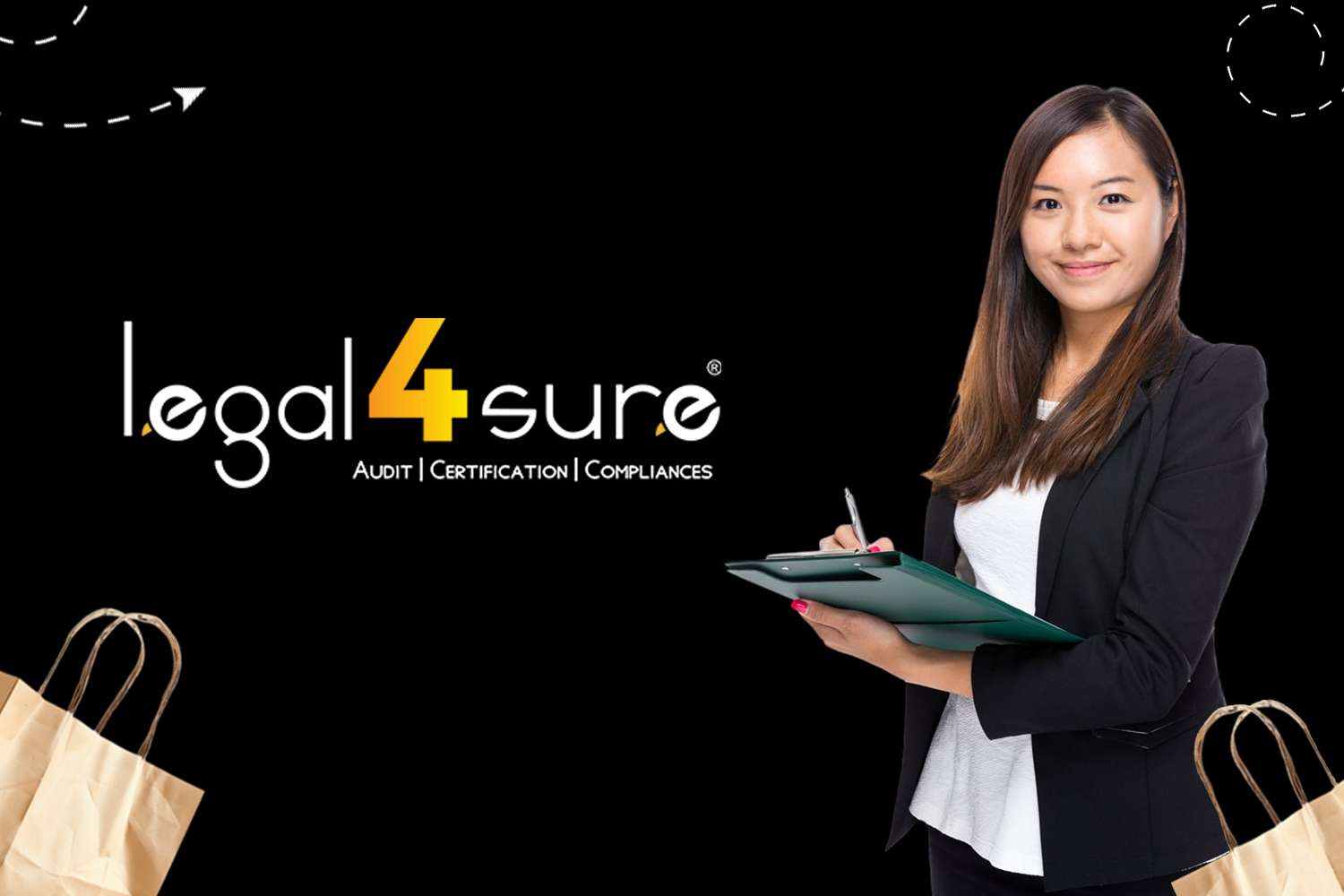
Cost Breakdown of BRCGS Certification for Paper Bag Factories
Cost Component | Estimated Cost (USD) |
---|---|
Application Fee | $1,000 – $2,500 |
Audit Fee (Annual) | $3,000 – $6,000 |
Consultant Fee (Optional) | $2,000 – $5,000 |
Employee Training | $1,500 – $3,000 |
Compliance Upgrades | $5,000 – $10,000 |
Total Estimated Cost | $12,500 – $26,500 |
Note: Costs vary based on location, auditor selection, and additional compliance upgrades.
Learn More: BRCGS Certification Cost
Case Studies: Successful BRCGS Certification in Paper Bag Factories
Case Study 1: GreenPack Solutions (India)
➜ Challenge: GreenPack Solutions, a mid-sized paper bag manufacturer, faced rejection from major retailers due to lack of compliance.
➜ Solution: They implemented BRCGS standards, trained employees, and upgraded equipment.
➜ Result: Achieved BRCGS certification in 8 months and secured contracts with large retailers like Flipkart and Big Bazaar.
Case Study 2: EcoBag Industries (UK)
➜ Challenge: Struggled with maintaining consistent quality across multiple production units.
➜ Solution: Introduced automated quality control measures and adopted sustainable sourcing practices.
➜ Result: Expanded exports to EU and North America, increasing revenue by 40% in 12 months.
How to Get BRCGS Certified: Step-by-Step Process
- Checking current processes to find gaps – Find areas of gaps and improve accordingly.
- Employee Training – Teaching employees the right skills and safety practices.
- Implement Quality Controls – Making sure every product meets high standards.
- Documentation & Internal Audits – Maintain records and conduct internal audits.
- Schedule an External Audit – Select a BRCGS-approved certification body.
- Obtain Certification – If successful, receive BRCGS certification (valid for 1 year).
- Annual Renewal & Continuous Improvement – Ensure ongoing compliance.
Read More: BRCGS Packaging Certification -Everything You Need To Know
Final Thoughts
BRCGS certification is not just a compliance requirement- it is a competitive advantage for paper bag factories. It opens doors to global markets, builds trust with top brands, and make sure long-term business sustainability.
Get Certified with Our Expert Assistance!
At Legal4sure, we specialize in guiding paper bag manufacturers through the BRCGS certification process. With over 50 successful BRCGS certifications, we provide end-to-end compliance support, employee training, documentation, and audit preparation.
Contact us at +91 9310655040 today to start your BRCGS certification journey!